Maximizing Efficiency and Accuracy with MRP Software: A Comprehensive Guide
In the realm of manufacturing, efficiency, accuracy, and timeliness are paramount. To meet these demands, many organizations turn to Material Requirements Planning (MRP) software. In this article, we’ll explore MRP software in detail, including its functionalities, benefits, implementation considerations, and key features that can transform manufacturing operations.
MRP Software
Material Requirements Planning (MRP) software is a specialized tool designed to help manufacturers plan, track, and manage their materials, components, and production processes. At its core, MRP software analyzes demand, forecasts requirements, schedules production, and optimizes inventory levels to ensure smooth operations and minimize costly inefficiencies.
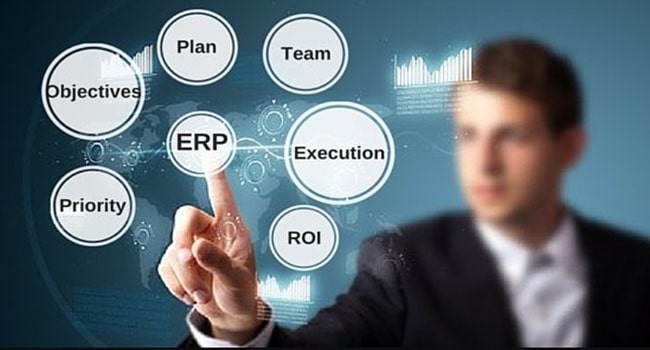
Key Features of MRP Software
- Inventory Management: MRP software provides real-time visibility into inventory levels, allowing manufacturers to track stock levels, monitor usage rates, and identify shortages or excesses. This ensures that materials are available when needed, minimizing production disruptions and stockouts.
- Bill of Materials (BOM) Management: MRP software maintains a centralized repository of Bill of Materials, which lists all the components, subassemblies, and raw materials required to manufacture a product. By managing BOMs effectively, manufacturers can ensure accurate planning, costing, and production scheduling.
- Demand Forecasting: MRP software utilizes historical data, sales forecasts, and customer orders to predict future demand for materials and products. By forecasting demand accurately, manufacturers can optimize inventory levels, reduce carrying costs, and meet customer requirements more effectively.
- Production Planning and Scheduling: MRP software generates production schedules based on demand forecasts, available capacity, and lead times for materials and resources. This ensures that production processes are optimized, bottlenecks are minimized, and orders are fulfilled on time.
- Procurement and Purchase Order Management: MRP software automates the procurement process by generating purchase orders for materials based on demand forecasts and inventory levels. This streamlines purchasing, reduces lead times, and ensures that materials are procured at optimal prices.
- Shop Floor Control: MRP software provides tools for monitoring and managing production activities on the shop floor in real-time. This includes tracking work orders, updating production status, allocating resources, and resolving production issues promptly.
- Reporting and Analytics: MRP software generates comprehensive reports and analytics on key performance indicators (KPIs) such as inventory turnover, on-time delivery, production efficiency, and cost variance. This allows manufacturers to identify trends, assess performance, and make data-driven decisions to improve operations.
Benefits of MRP Software
- Improved Inventory Management: MRP software helps manufacturers optimize inventory levels, reduce carrying costs, and minimize stockouts by ensuring that the right materials are available at the right time.
- Enhanced Production Planning: By automating production planning and scheduling, MRP software enables manufacturers to optimize production processes, minimize lead times, and improve on-time delivery performance.
- Cost Savings: MRP software helps manufacturers reduce costs associated with excess inventory, stockouts, overtime labor, and rush orders by optimizing resource utilization and streamlining operations.
- Increased Accuracy and Efficiency: MRP software automates repetitive tasks, eliminates manual errors, and ensures data accuracy, leading to improved operational efficiency and productivity.
- Better Decision-Making: With access to real-time data, analytics, and insights, MRP software empowers manufacturers to make informed decisions, anticipate market trends, and respond quickly to changing customer demands.
Implementation Considerations
Implementing MRP software requires careful planning, preparation, and collaboration between different departments and stakeholders within the organization. Key considerations include:
- Data Accuracy and Cleanliness: Ensure that master data such as BOMs, inventory records, and lead times are accurate and up-to-date before implementing MRP software.
- User Training and Adoption: Provide comprehensive training and support to users to ensure that they understand how to use the MRP software effectively and leverage its full capabilities.
- Integration with Existing Systems: Ensure that MRP software integrates seamlessly with existing enterprise systems such as ERP, CRM, and accounting software to facilitate data exchange and workflow automation.
- Customization and Configuration: Tailor the MRP software to meet specific business requirements, workflows, and industry standards through customization and configuration options.
- Continuous Improvement: Monitor and evaluate the performance of MRP software regularly, identify areas for improvement, and implement enhancements to maximize its value and impact on manufacturing operations.
Conclusion
MRP software plays a crucial role in optimizing manufacturing operations, improving efficiency, and driving growth in today’s competitive marketplace. By automating material planning, production scheduling, and inventory management processes, MRP software enables manufacturers to minimize costs, maximize resource utilization, and deliver products to market faster and more efficiently.
With the right MRP software solution and implementation strategy, manufacturers can gain a competitive edge, adapt to changing market conditions, and thrive in an increasingly dynamic and complex manufacturing environment.